Inputs and chemical products for plating, silver plating and chromium plating
Chrome plating products
“We formulate our own products, to achieve the best chemical reaction in the silver plating of parts.”
For more than 10 years we have been constantly evolving our products and paints for chrome plating and silver plating of parts. We are manufacturers of all the Chrome Plating Systems we sell, as well as of the products for chrome plating. We develop and test everything: from the base coat, the pre-activator, activator, silver, to the final varnish, essential to achieve the adherence and durability we are looking for in our paints.
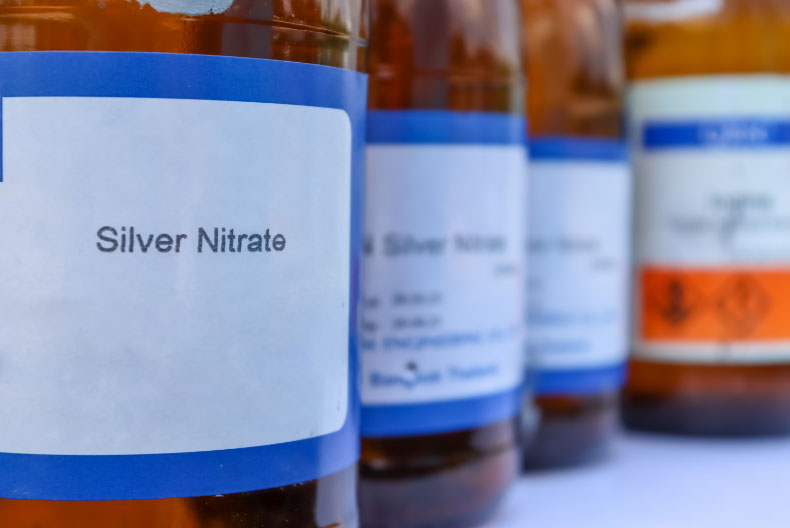
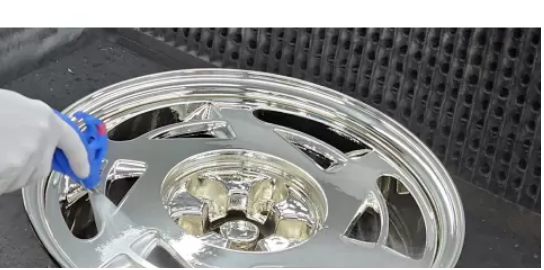
By means of the correct and precise formulation, we make the chemical reaction of the silver nitrate stabilize the silver plating applied on the base coat, of which we have previously opened the pore with our Preactivator or Wetting Agent, thus saving us the always uncomfortable and dangerous step of flaming, especially complex in large or delicate parts, such as plastic parts.
CHROME TESTING AND DURABILITY
At Racing Colors we understand that it is just as important that the chrome finish is as perfect and shiny as possible, as it is that it is as durable and resistant as we can get. To this end, we carry out countless resistance tests on our products, testing them under the worst possible conditions, to evaluate the resistance of the parts in conditions of humidity, shocks or impacts, immersion in hot and cold water, exposure to the sun,…
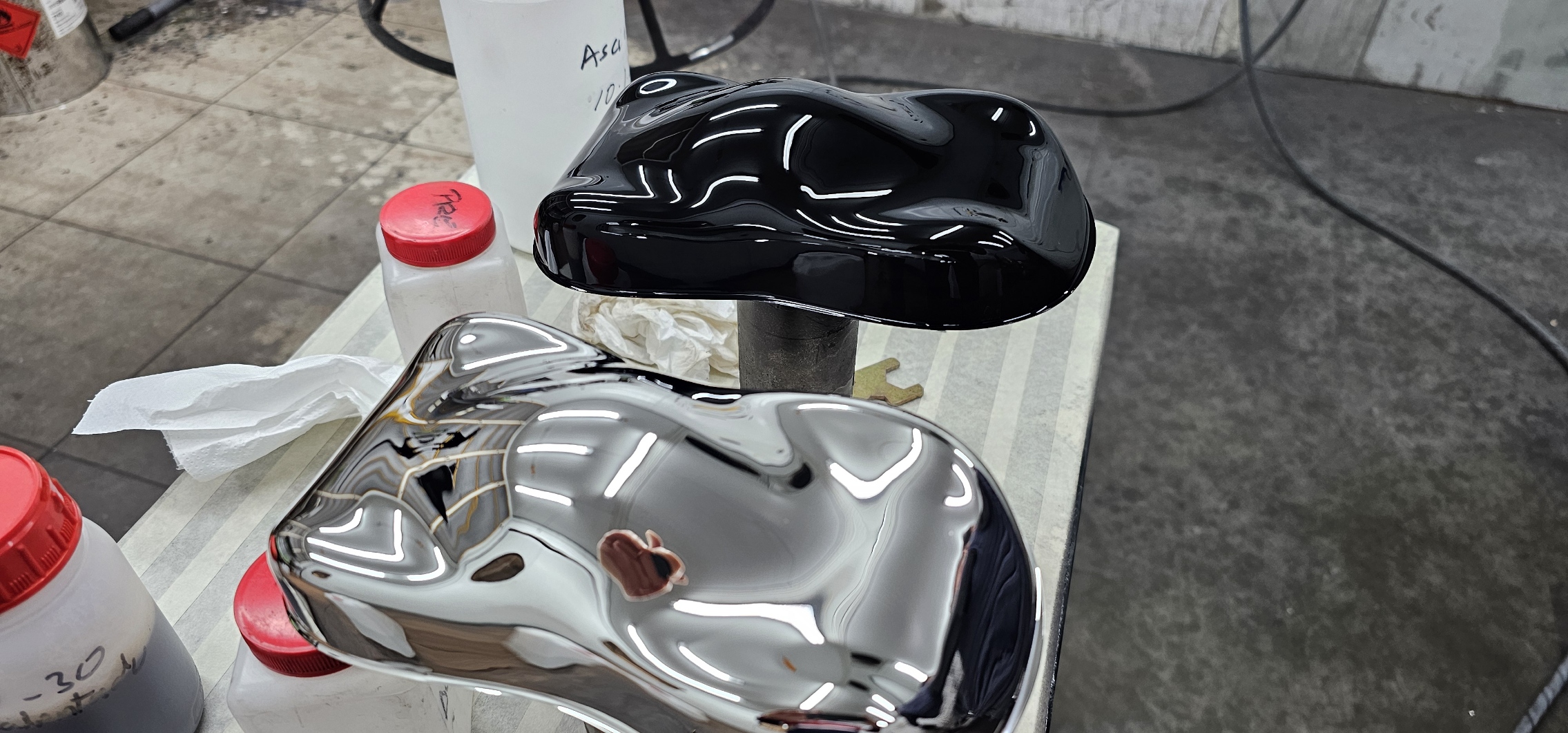
The procedure we normally perform is as follows:
– We take a PVC plate, sand it with fine sandpaper, and apply the base coat.
– We chrome plated the parts with the products selected for testing
– Then we dry it properly and carry out the tests.
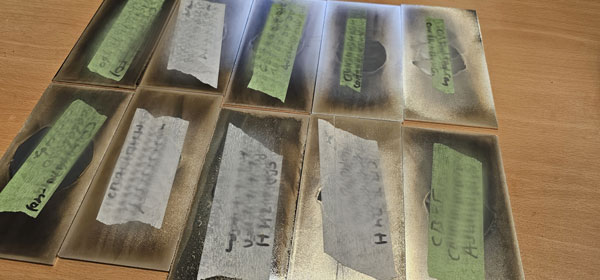
The tests to which we subject the parts are basically:
– UNE EN ISO 2409:2007 dry grating cut, according to ASTM D3359, ISO 2409 adhesion test standard with NK2000 adhesion tester. This test is carried out 24 hours after varnishing the piece when it is completely dry. Also in this case we test the packaging or sealing of the pieces, to check that the varnish is dry enough so that it does not leave marks and can be shipped in just 1-2 days after chrome plating.
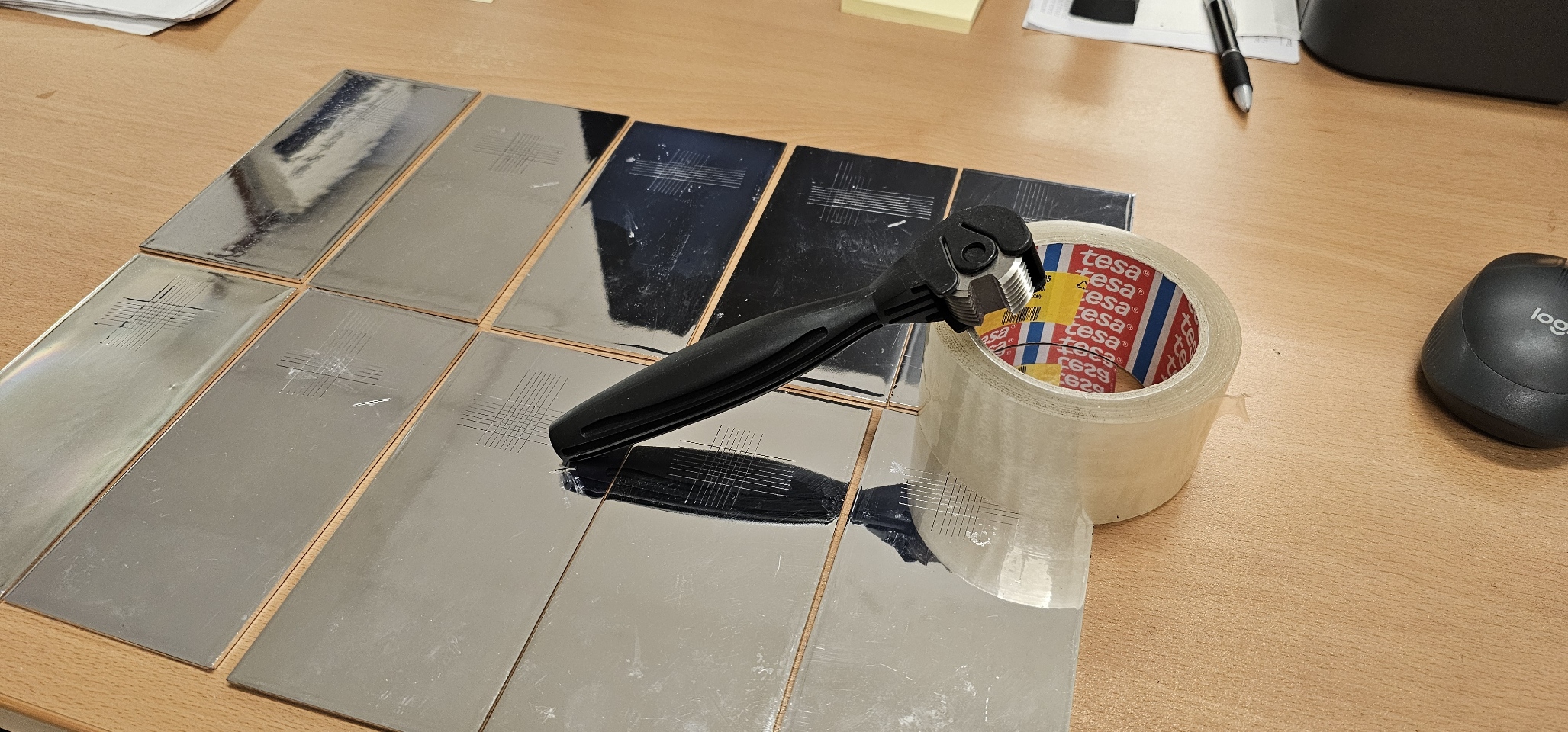
– Once this test is passed, the part is subjected to the immersion test for a period of 24 hours, completely submerging the scratched part, and the adhesion test is carried out again. This test is much more aggressive, as the water is penetrating through the lattice cut marks, simulating a hit or scrape on a real part that is in contact with rainwater outdoors.

Then we leave it in immersion for another 1 month to test the long-term durability, again immersing the scratched part completely in water to make the test as realistic and aggressive as possible.
We also subject the parts to several months of exposure to the sun, salt spray and Xenotest (U.V. / UVB test), to check their actual durability.
But the best proof is to have chromed thousands of parts for years and, with proper care, they still have the same chrome effect they had the first day they left the workshop.
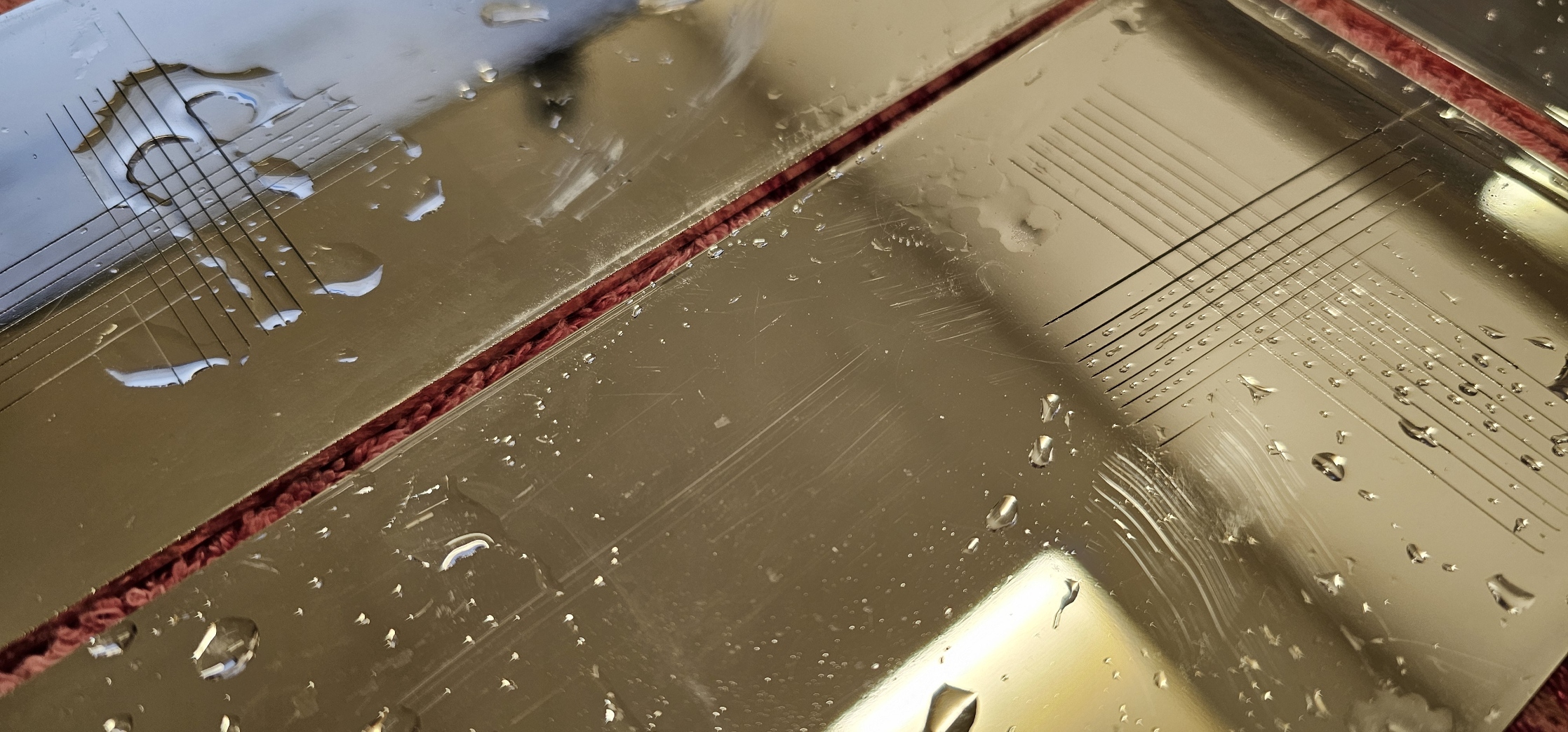
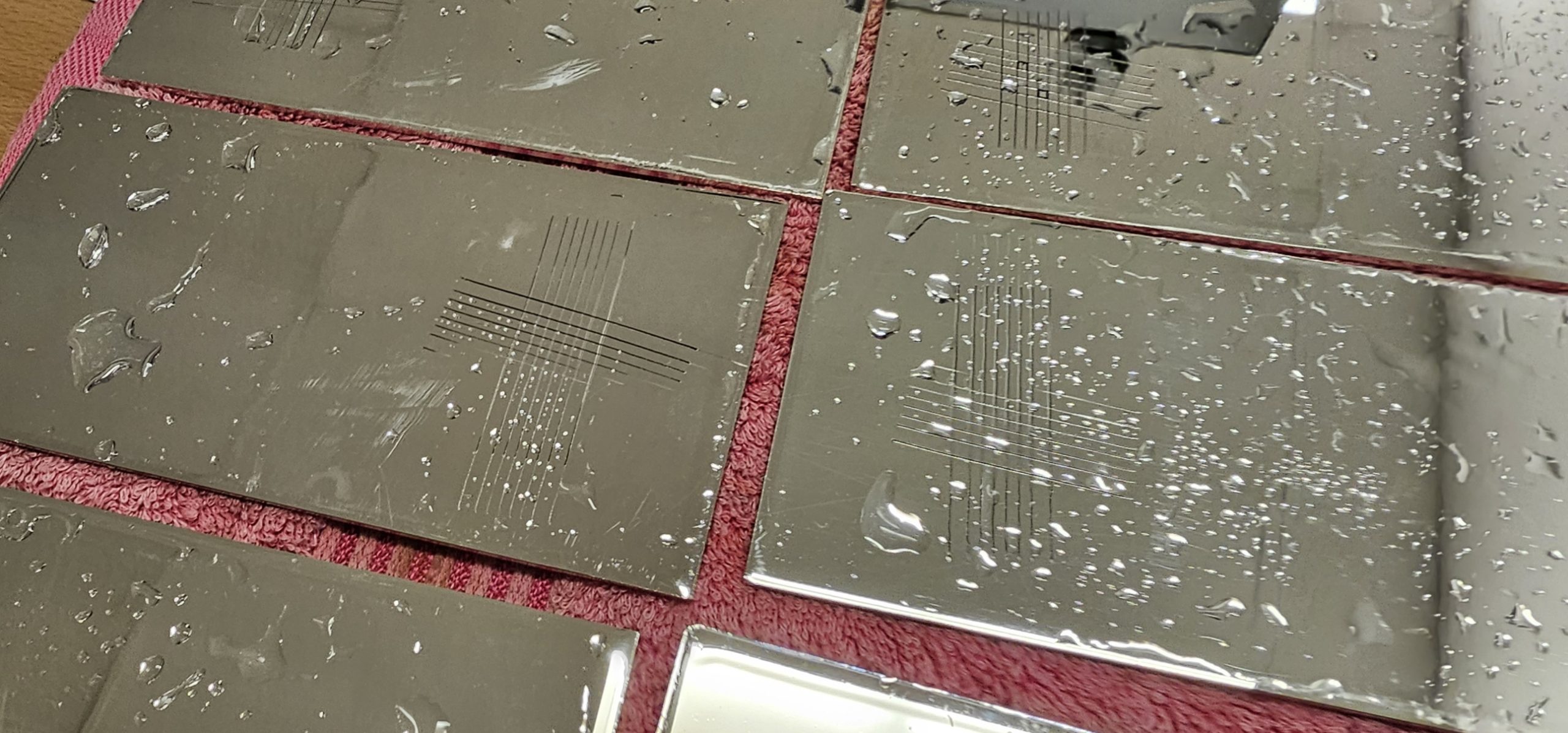
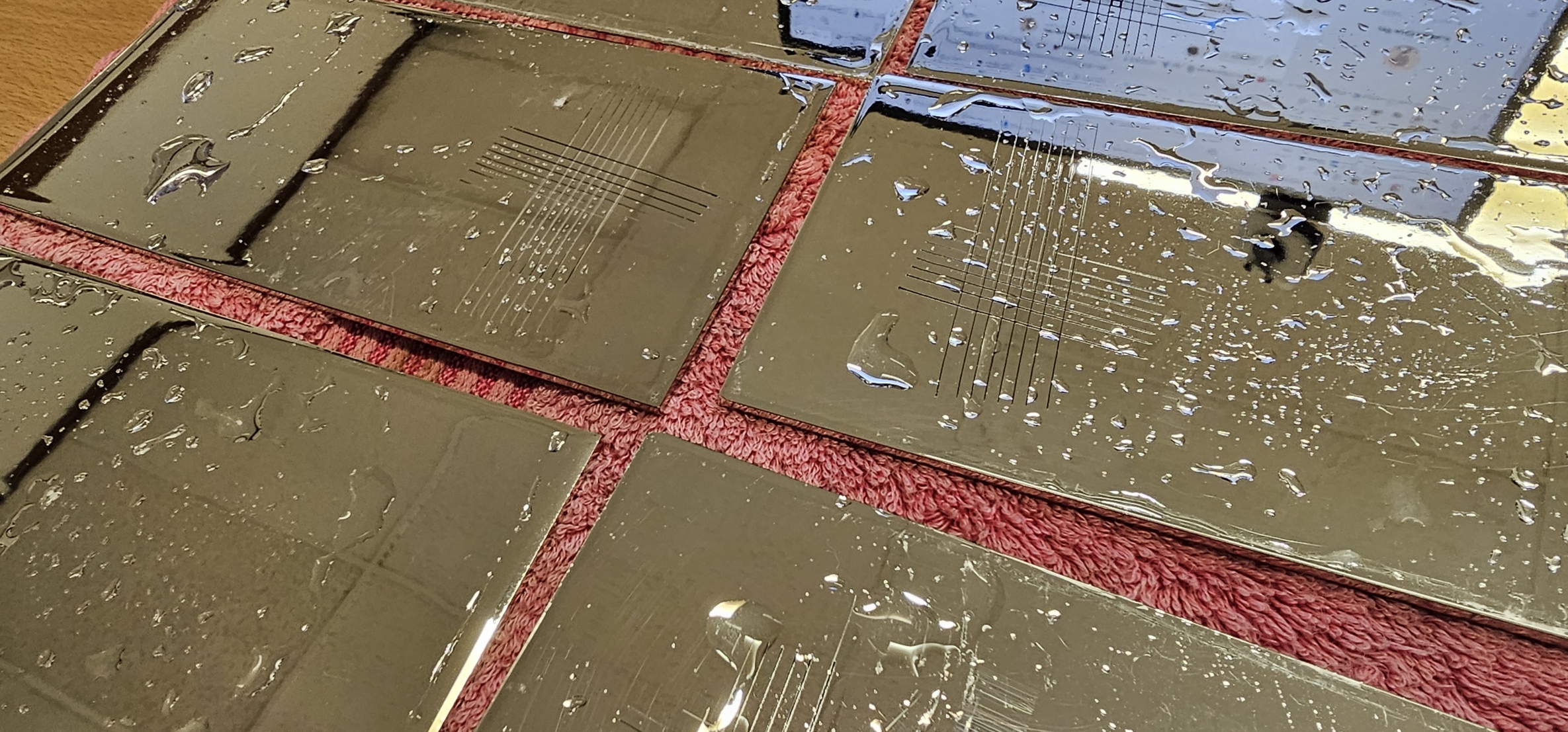
CHROME PLATING DEFECTS
It is important to follow all the application steps for a correct chrome plating result. Here we can see some of the most common most common mistakes when applying the chrome, and that are easily corrected with a correct application and drying of the products, and that we collect both in the Technical Manual and in the Complete Instruction Video, to learn all the steps to follow to achieve the chrome plating of any piece.
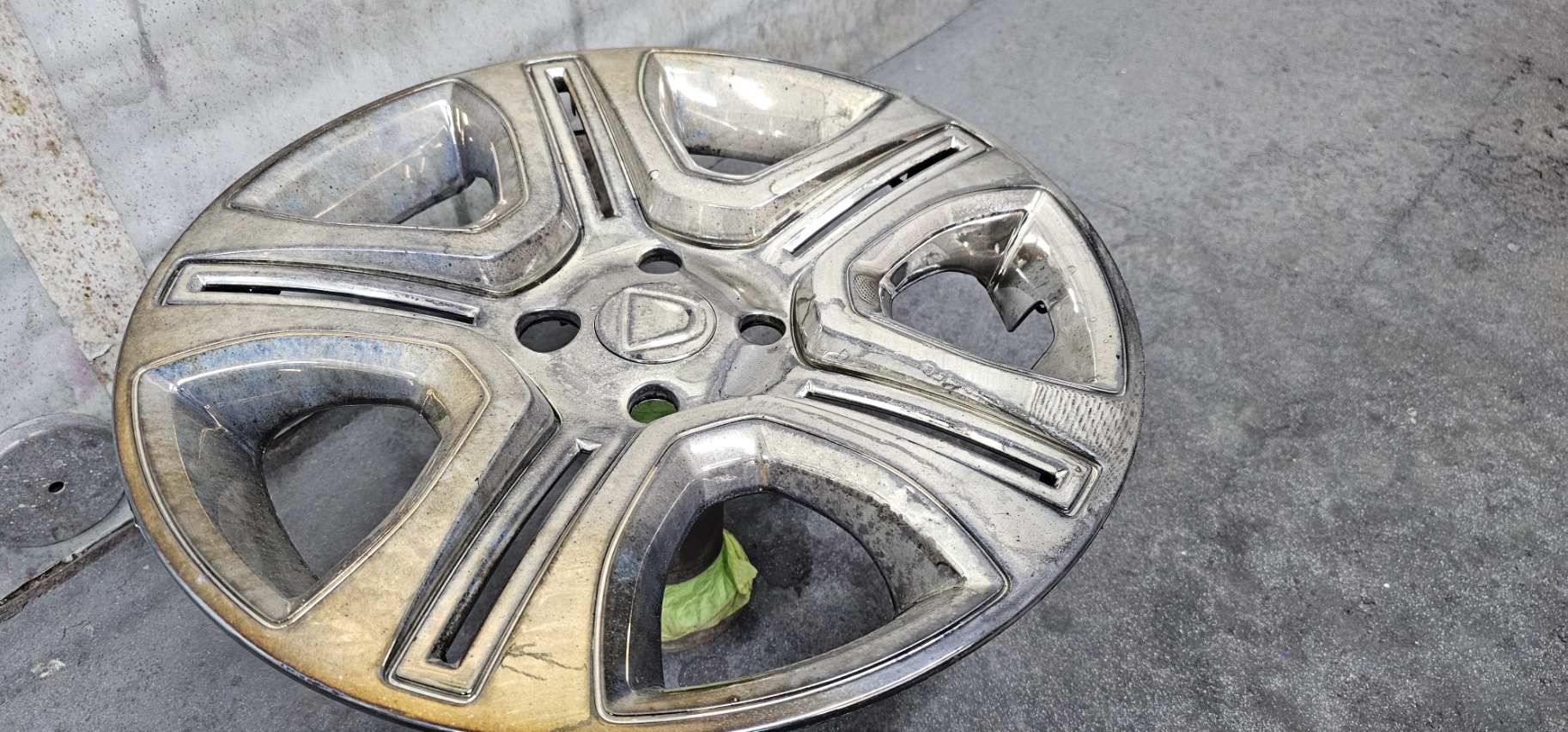
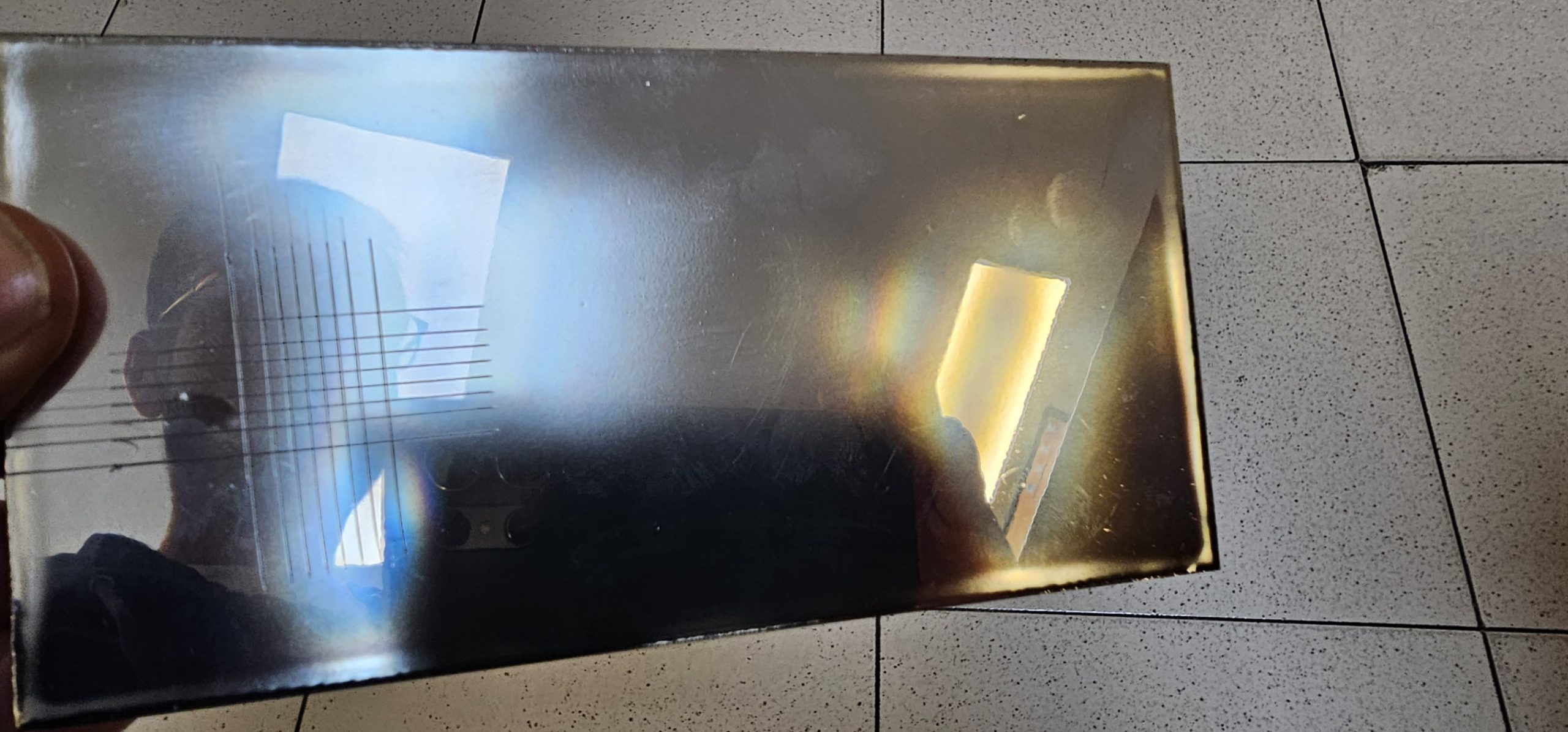
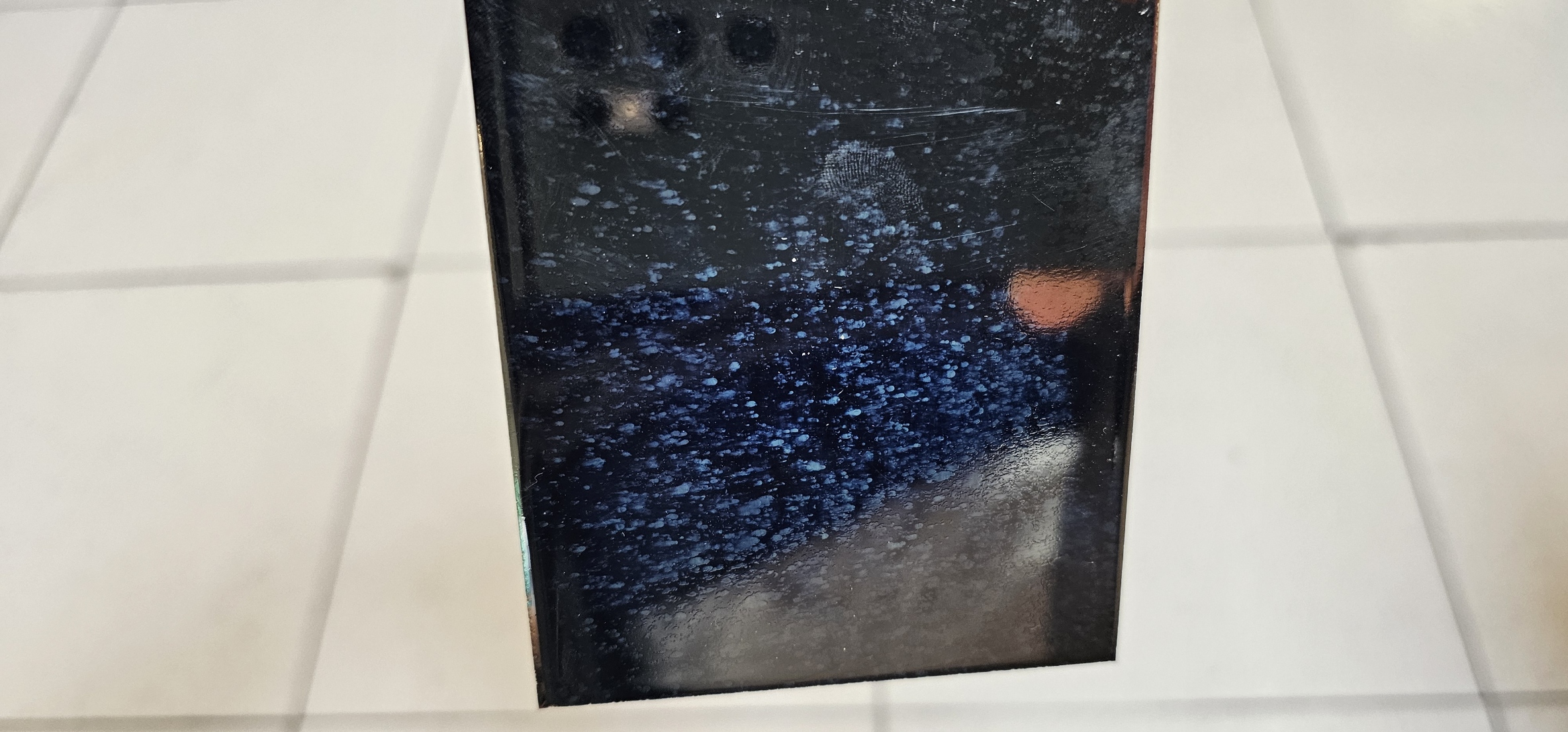
We can see in this image how the chrome is “cloudy” because the base coat is not sufficiently dry, or there are paints under the chrome that are not 100% evaporated.
Here you can see the varnished chrome, without having dried it sufficiently in the oven beforehand. All those marks from environmental humidity remain.
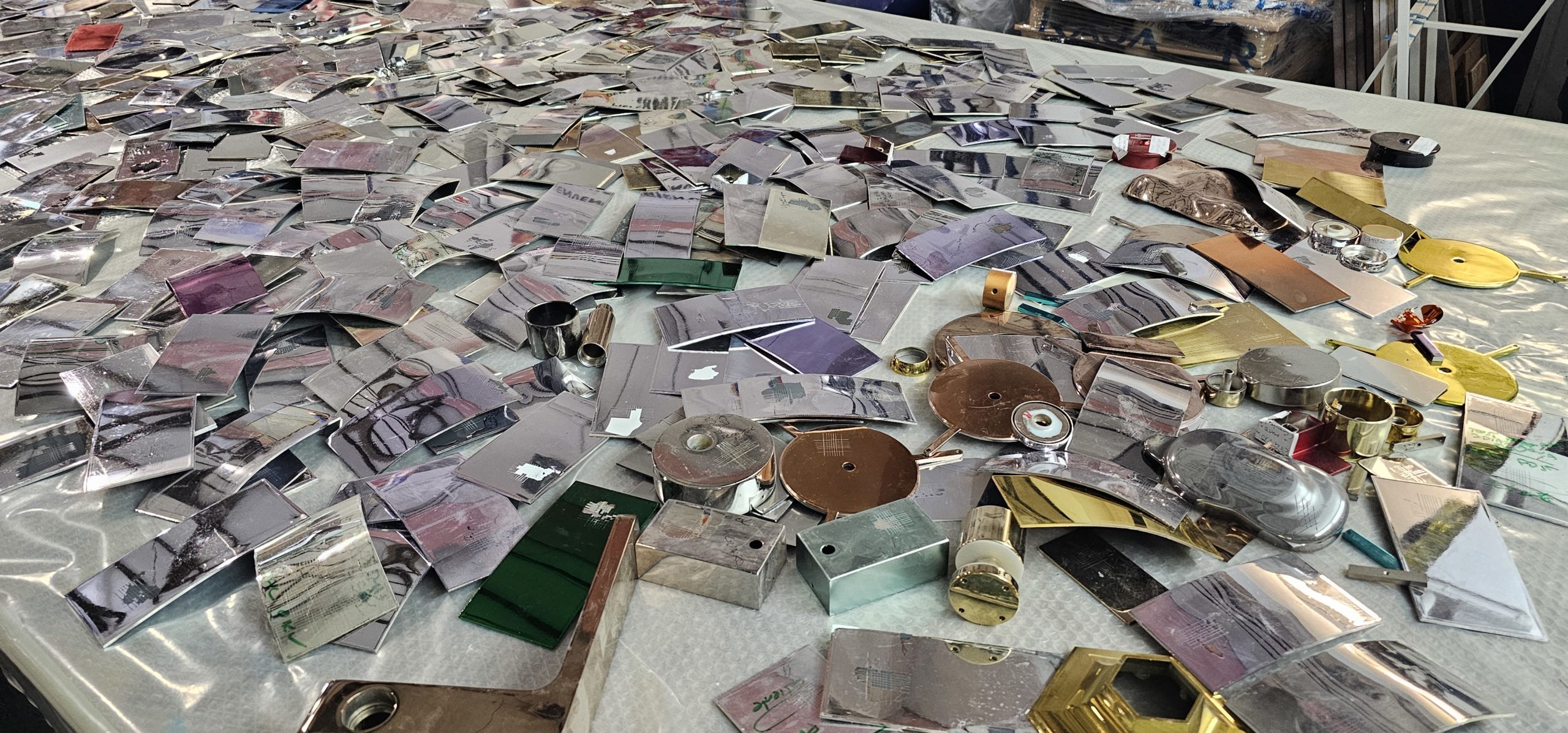
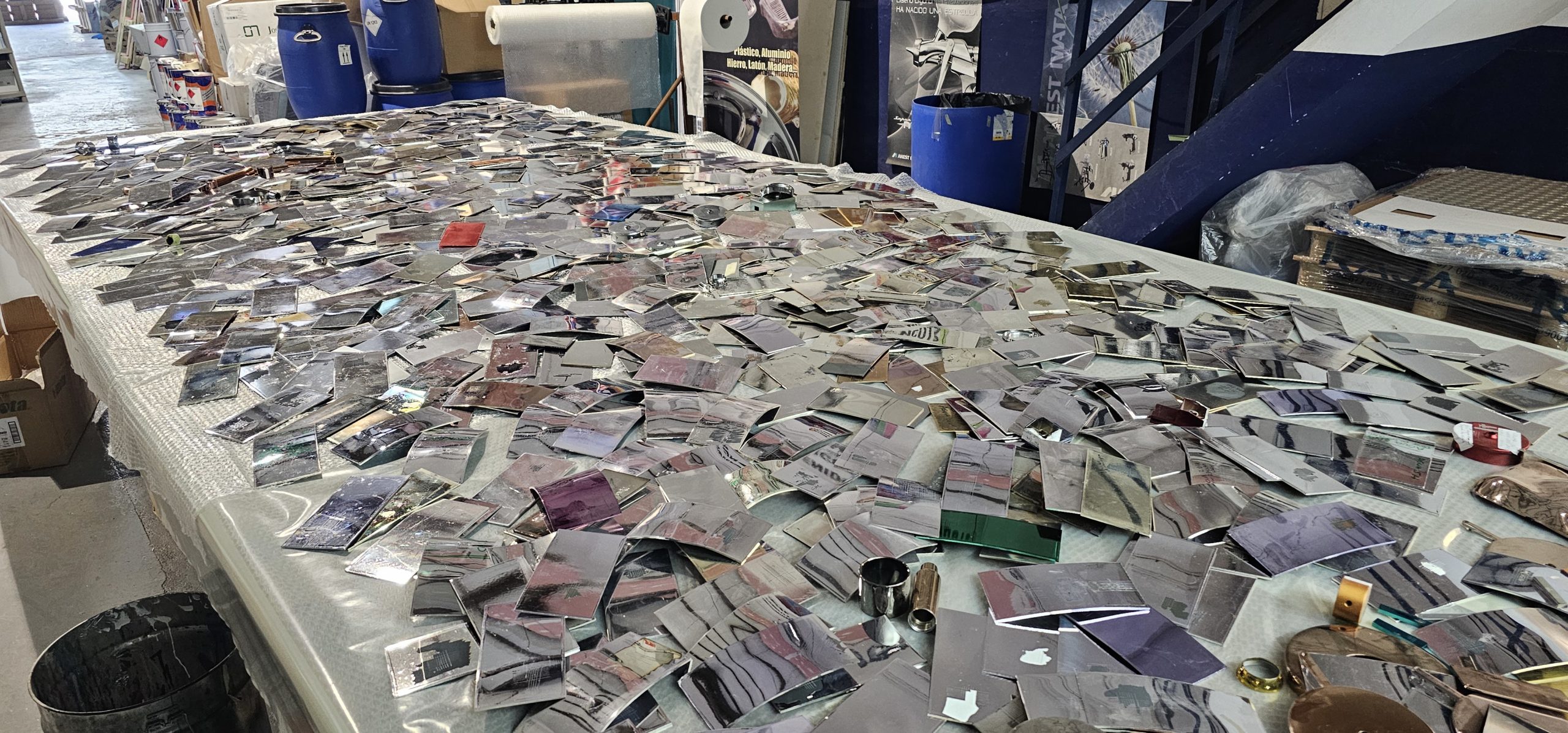
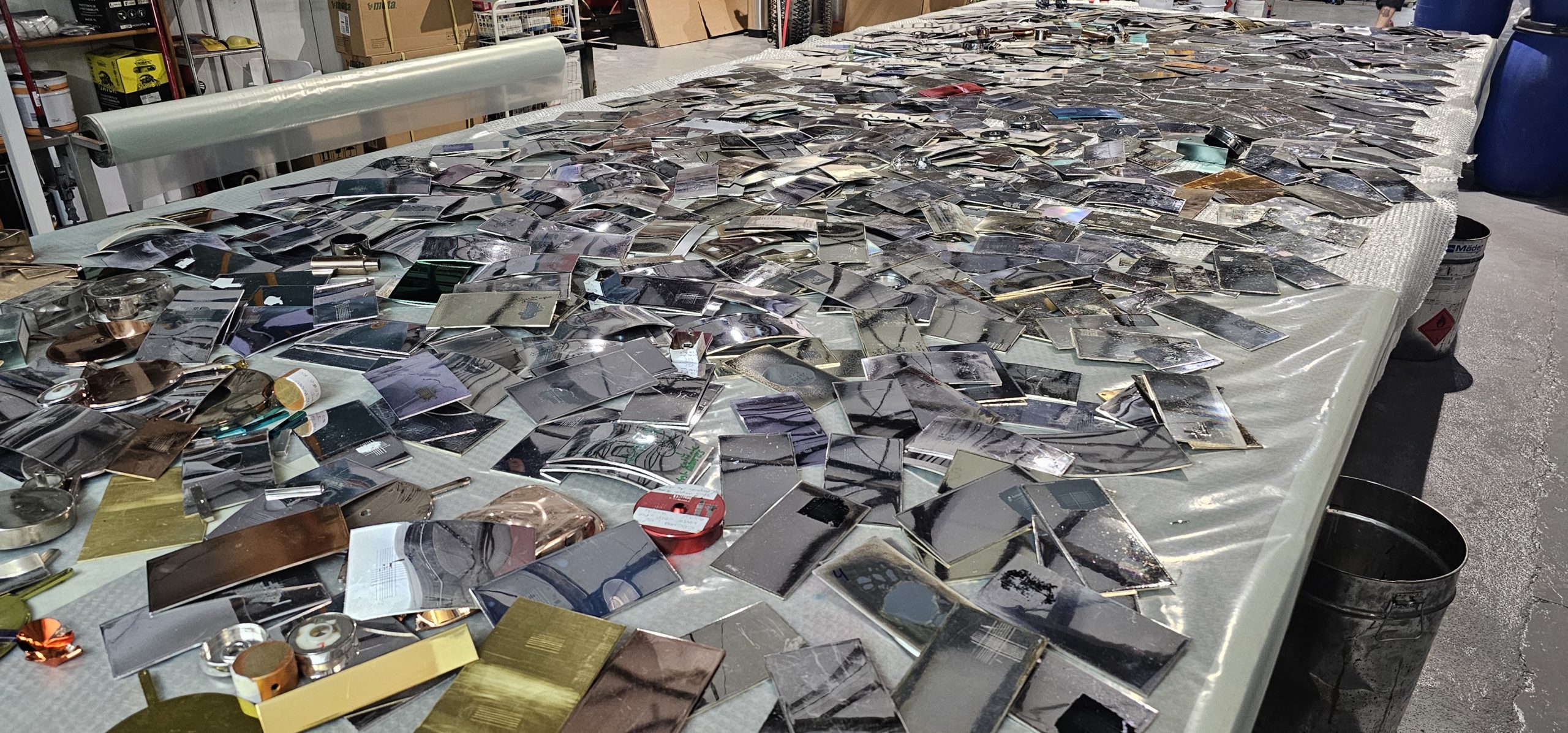
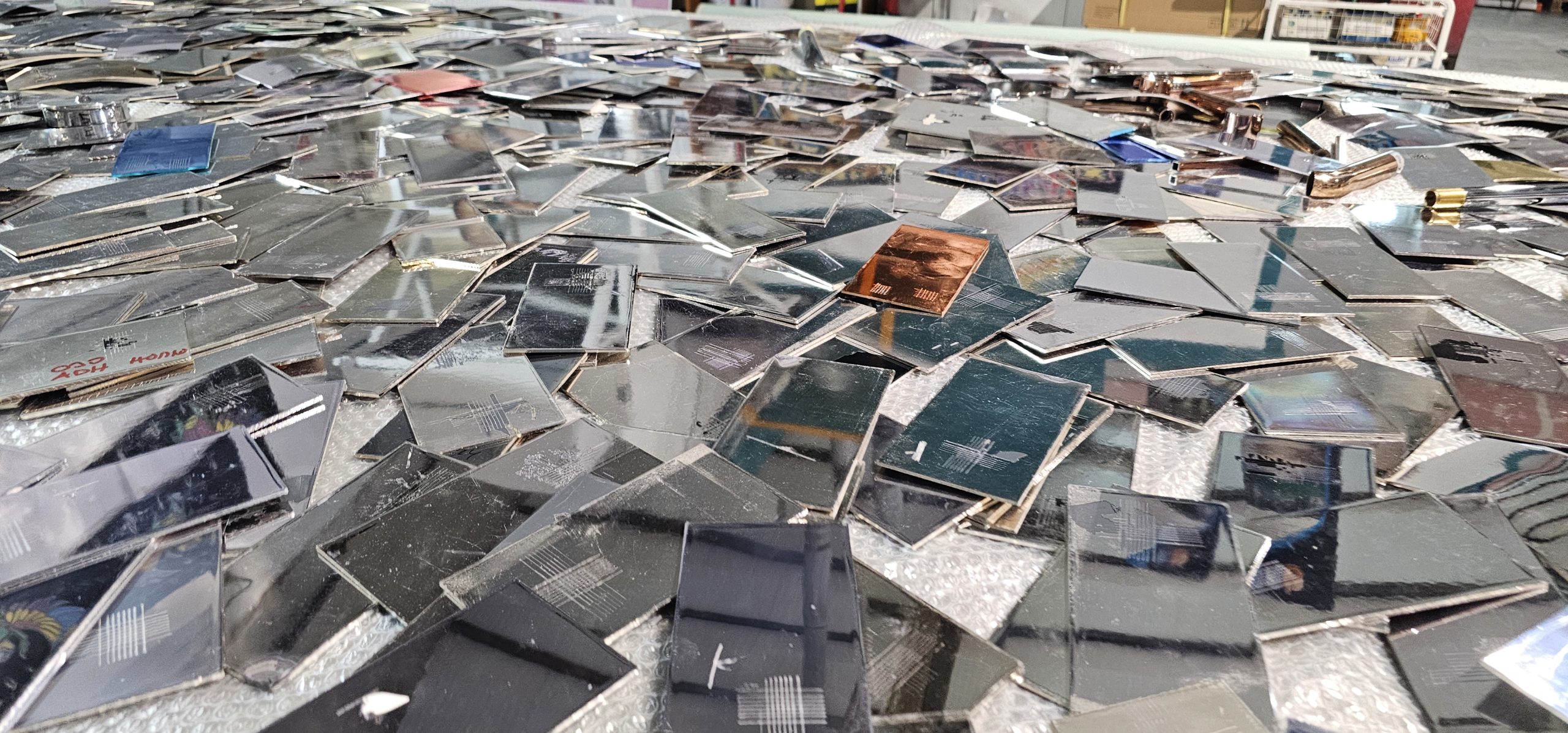
“We have performed thousands of tests on different substrates, to achieve, not only the best 100% mirror chrome effect, but the most durable in every way.”
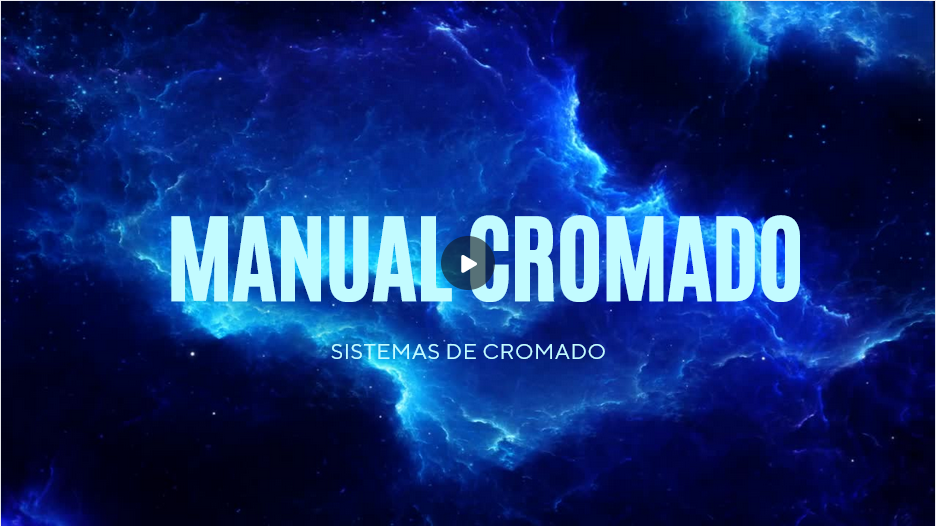
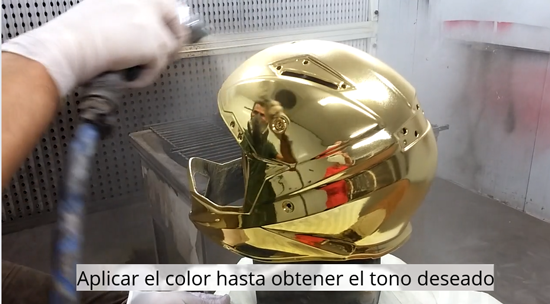
Thus, to achieve a quality chrome plating, without defects, clean, mirror, bright and with resistance both inside and outside, you must follow the instructions as shown in the Technical Manual supplied to all customers who use our products, as well as the extensive and detailed video demonstration, where we explain STEP BY STEP the process of preparing the parts, mixing the components, Application, Drying and Varnishing, as well as tips and advice for different types of parts and recommendations when chrome plating large or complicated parts.
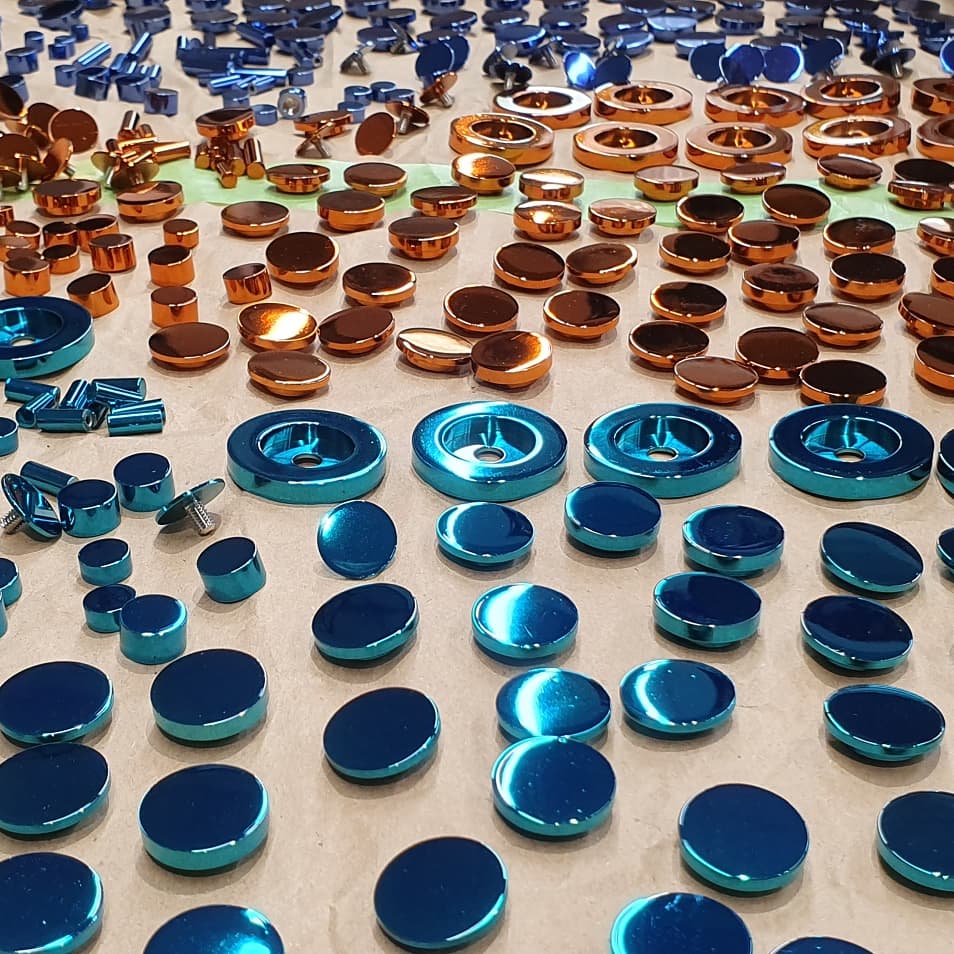
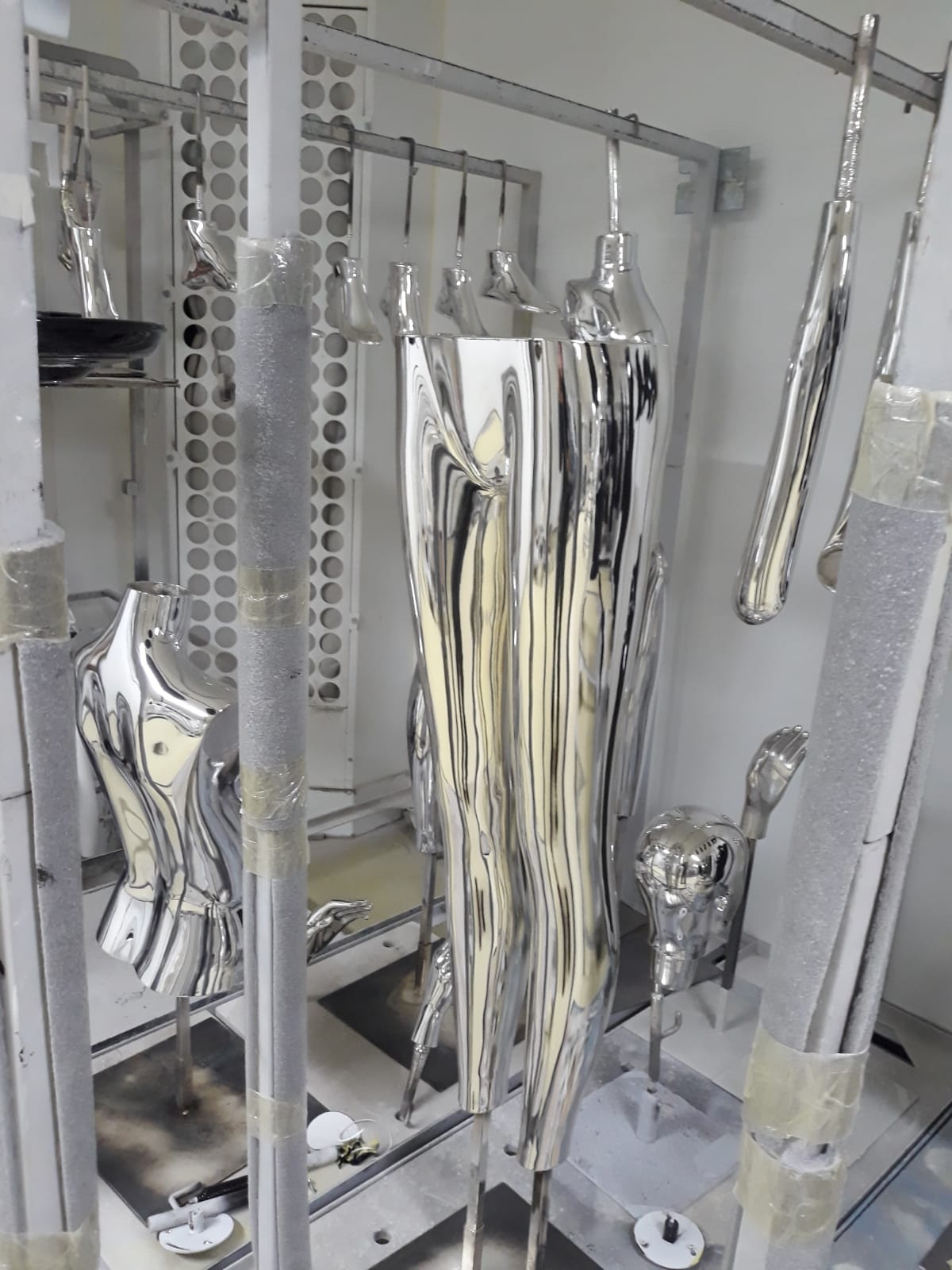
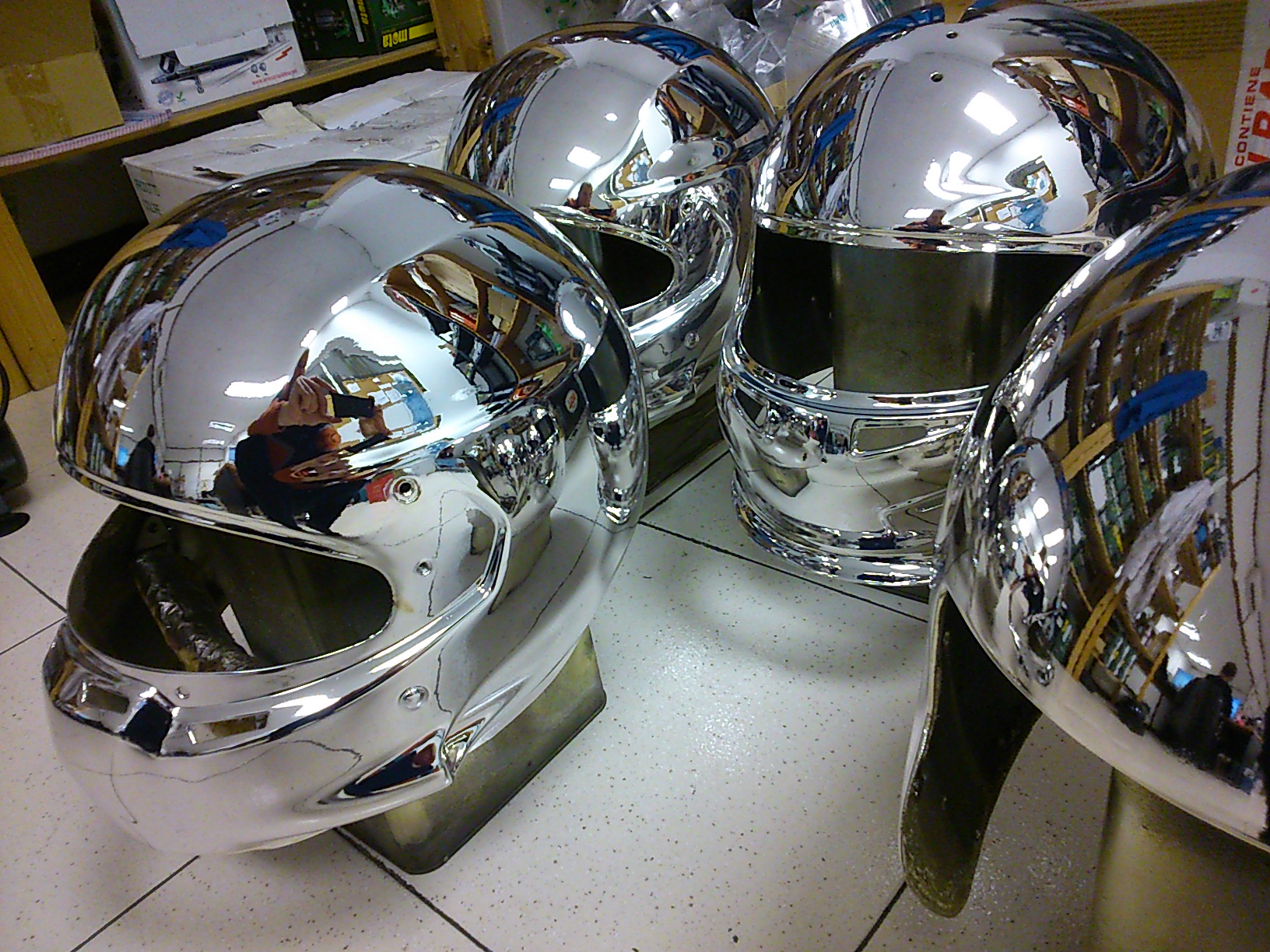
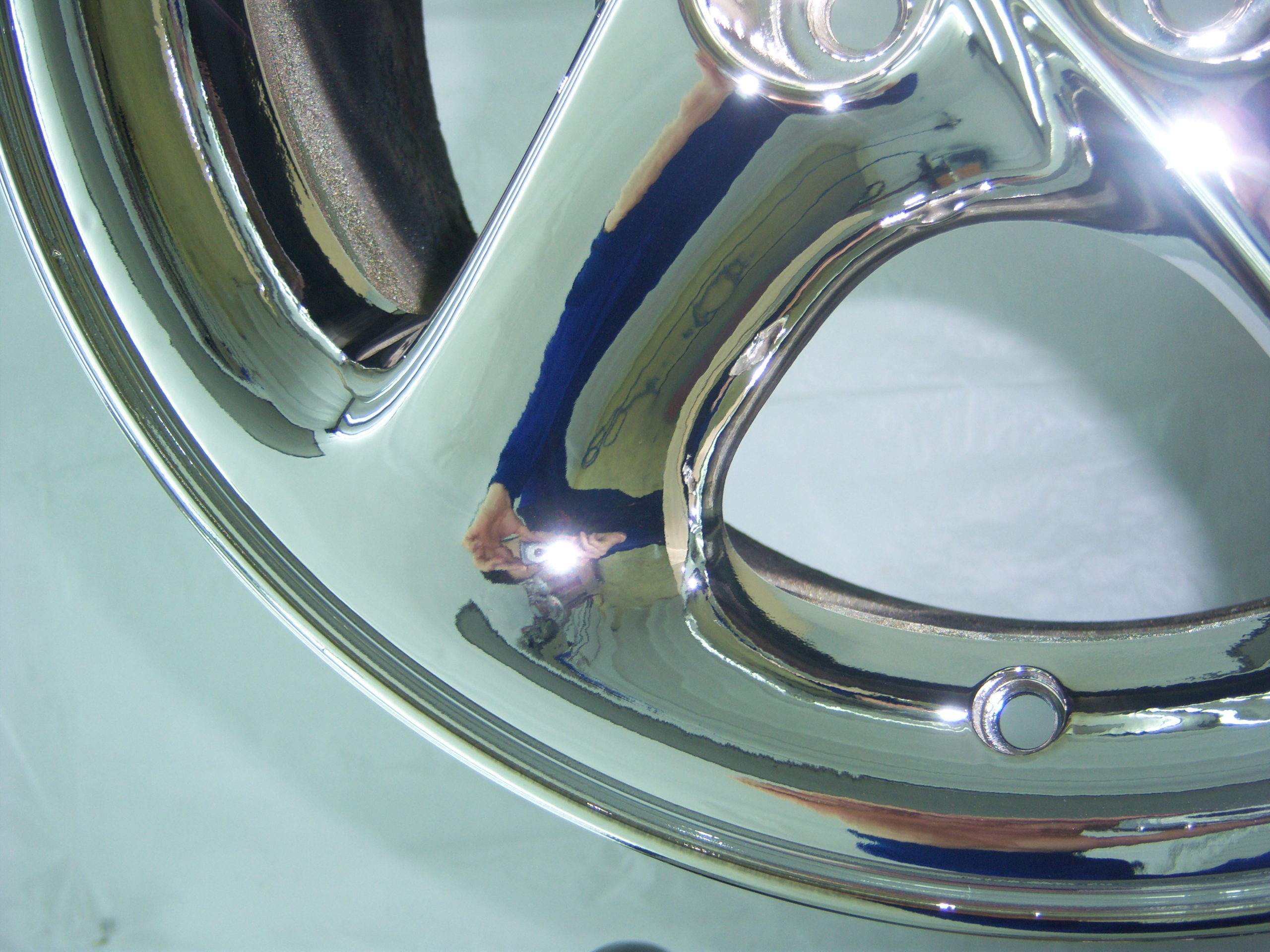
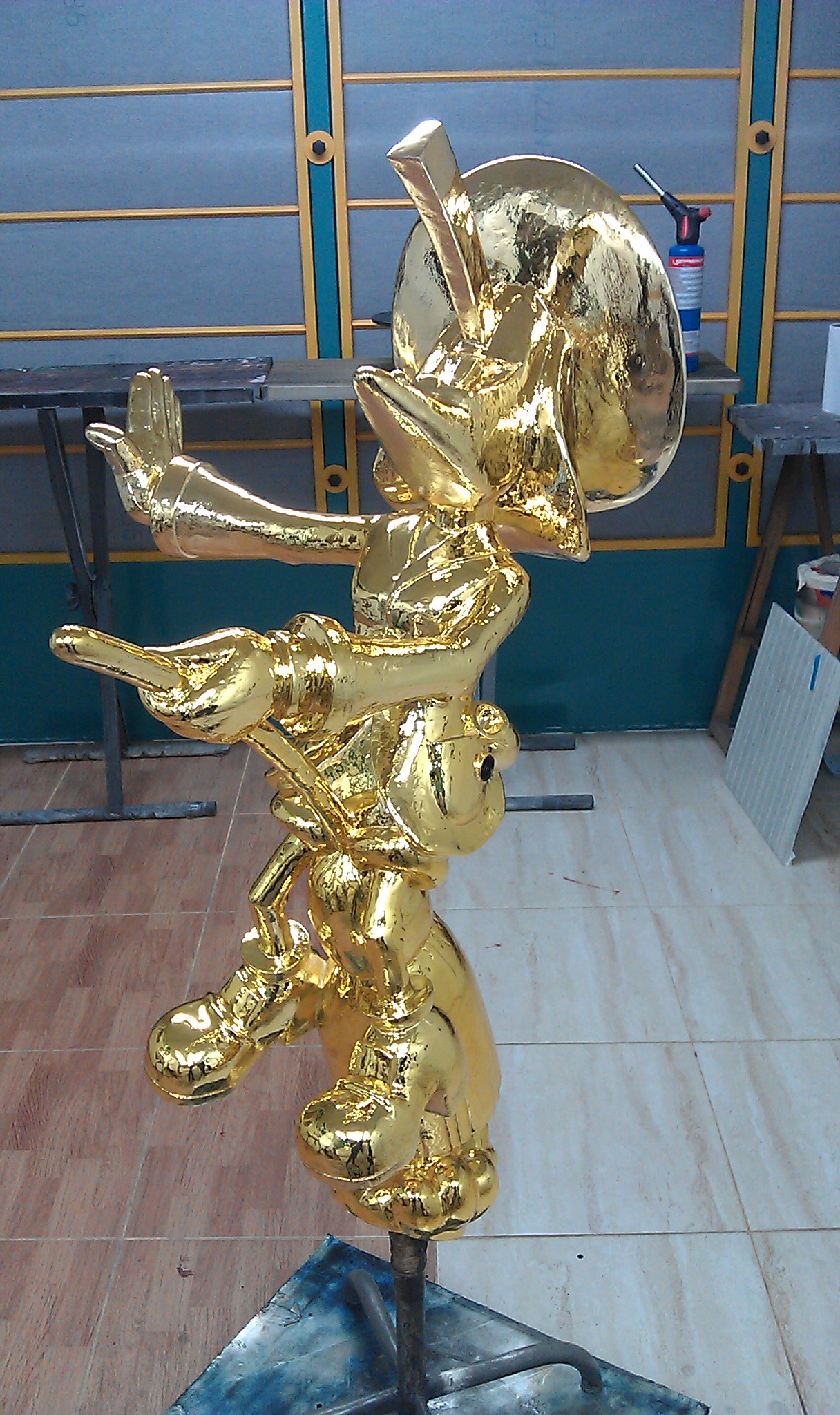
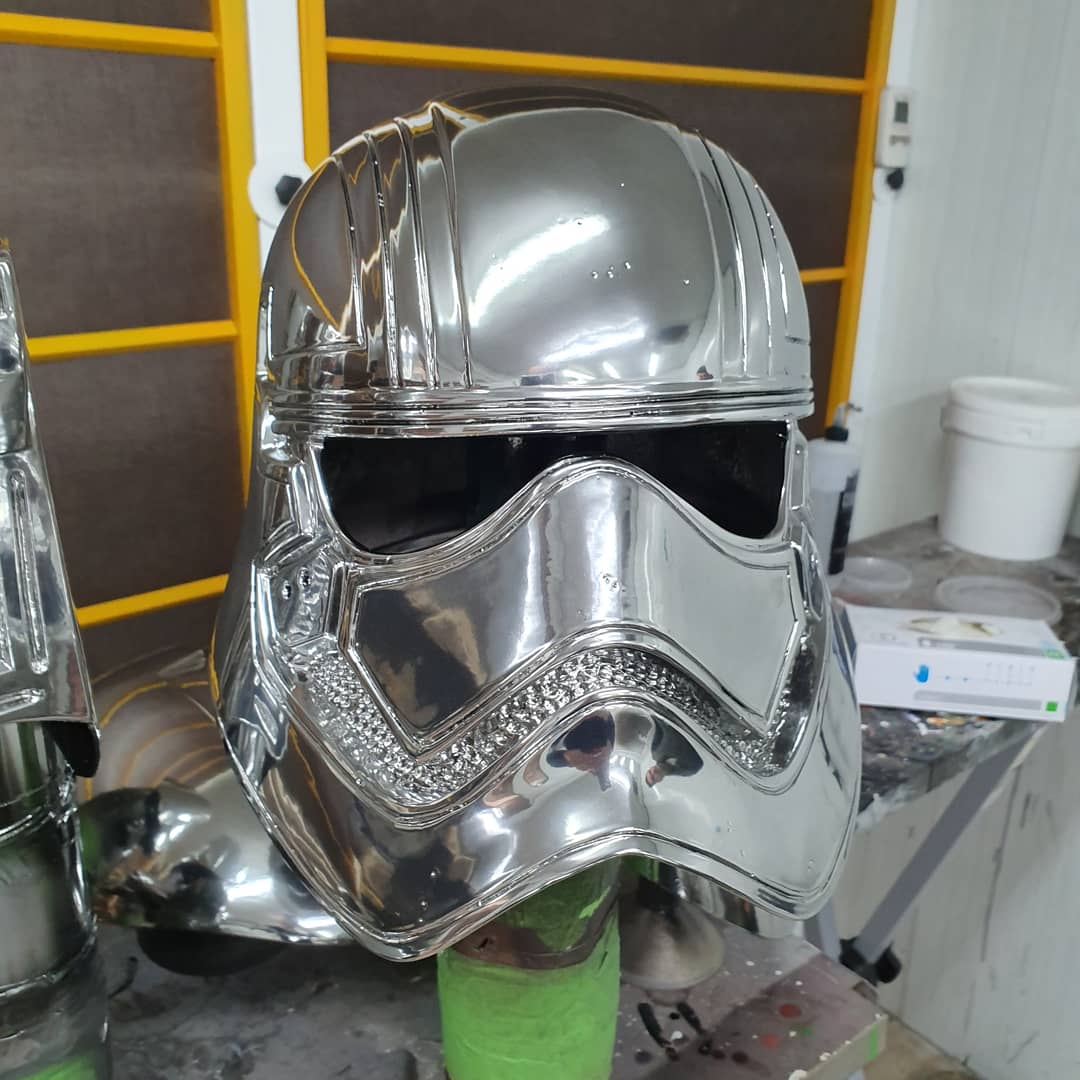
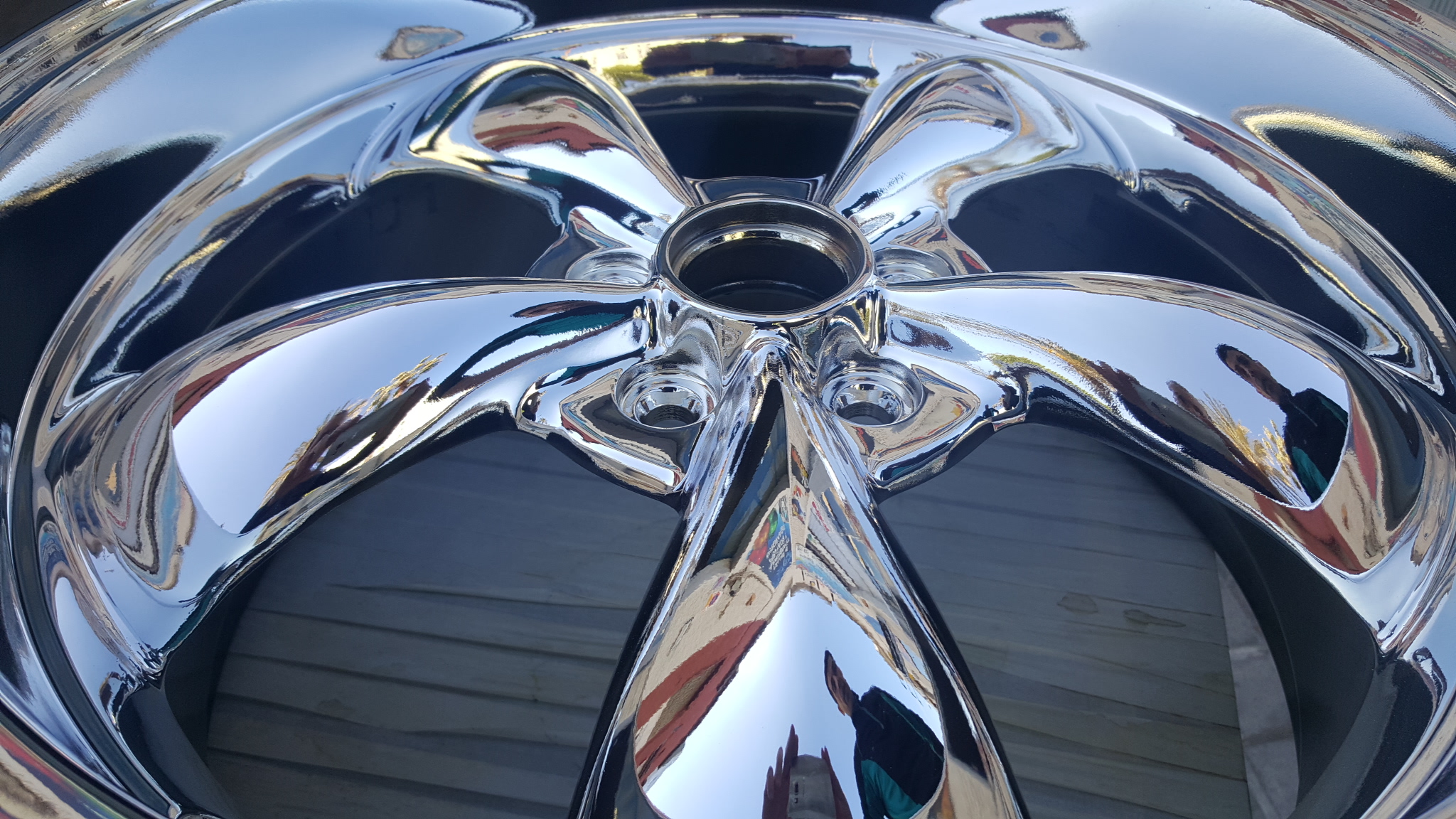
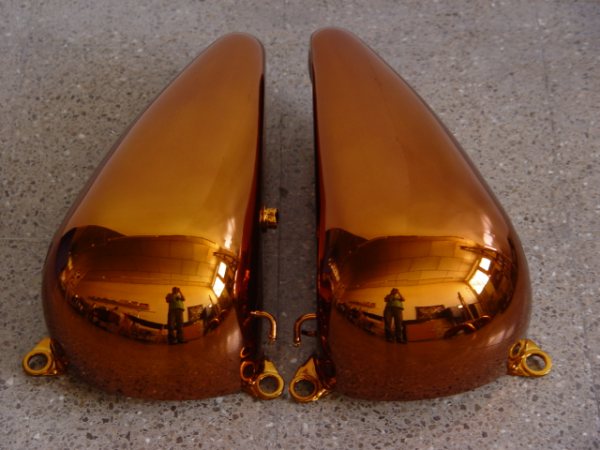
COLOR CHROME PLATING
One of our strengths is chrome plating in any color imaginable. We have 16 basics that you can see here: COLOR VARNISH FOR CHROME
Besides, an infinite number of colors can be created by mixing the basic ones with each other: copper, bronze, dark or light tones, intense or soft gold,…
Where can I get the products for chrome plating parts?
ONLINE STORE OF CHROME PLATING PRODUCTS